
16
2025
-
05
Yunt Power PCS and DCDC Modules Applied in the Energy Storage System of Workover Rigs
Author:
YUNT
Workover rigs, as core equipment in oilfields, still primarily rely on diesel engine drives at present. However, this power method suffers from high energy consumption, heavy pollution, and excessive noise, which contradicts the "Dual Carbon" goals (carbon peak and carbon neutrality). Therefore, electrification upgrades for workover rigs have become a major trend in future energy transition.
Conventional grid-powered workover rigs represent an initial attempt at electrification upgrades. Taking a 70-ton grid-powered workover rig as an example, its total motor power requirement reaches 240 kW, while standard wellhead transformers typically provide only 50 kVA or 75 kVA—far below the needed capacity. To compensate, an additional 200 kVA transformer must be installed. This not only increases costs but also introduces safety risks, severely hindering the broader adoption of grid-powered workover rigs.
To address this issue, the customer added a battery energy storage device based on the original grid-powered workover rig for capacity expansion and power compensation. By making rational use of the complementarity between the grid power and the electrical energy storage device, multiple working modes such as independent power supply, grid power supply, and combined power supply have been achieved. This not only improves the reliability of power supply but also effectively reduces energy consumption and pollution, meeting the requirements of the "dual carbon" goal.
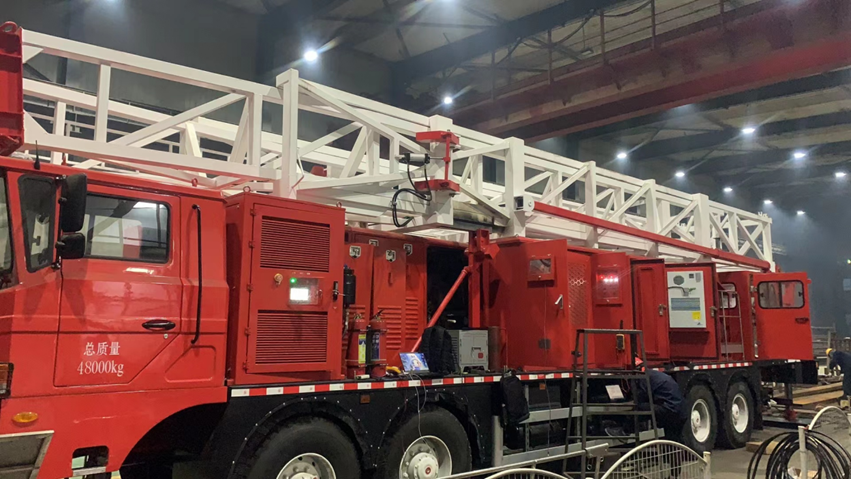
When the workover rig is performing workover operations, it is necessary to connect or unload each tubing, and the process of connecting or unloading each tubing forms a workover operation cycle. This operation mode obviously exhibits the characteristics of intermittent cycling. The working conditions of the workover rig are mainly divided into four parts: hoisting, unthreading, pipe arrangement, and lowering, and the power demand curves of each working condition are shown in the following figure:
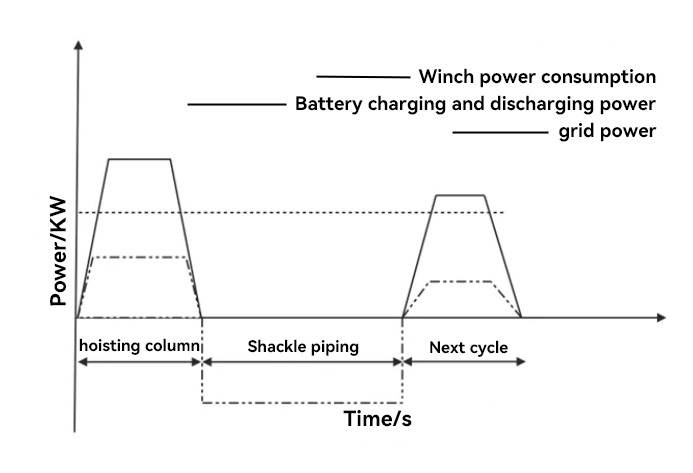
Figure 1 Power demand curves of each working condition of the workover rig
The power compensation system of the battery is utilized to compensate the power for the workover rig. The electrically energy-stored workover rig adopts the DC bus voltage control technology and is used in parallel with the wellhead transformer. The energy formed by the parallel connection of the grid power and the battery pack can fully meet the power demand of the workover operation, and the operation efficiency of this workover rig is superior to that of the traditional workover rig.
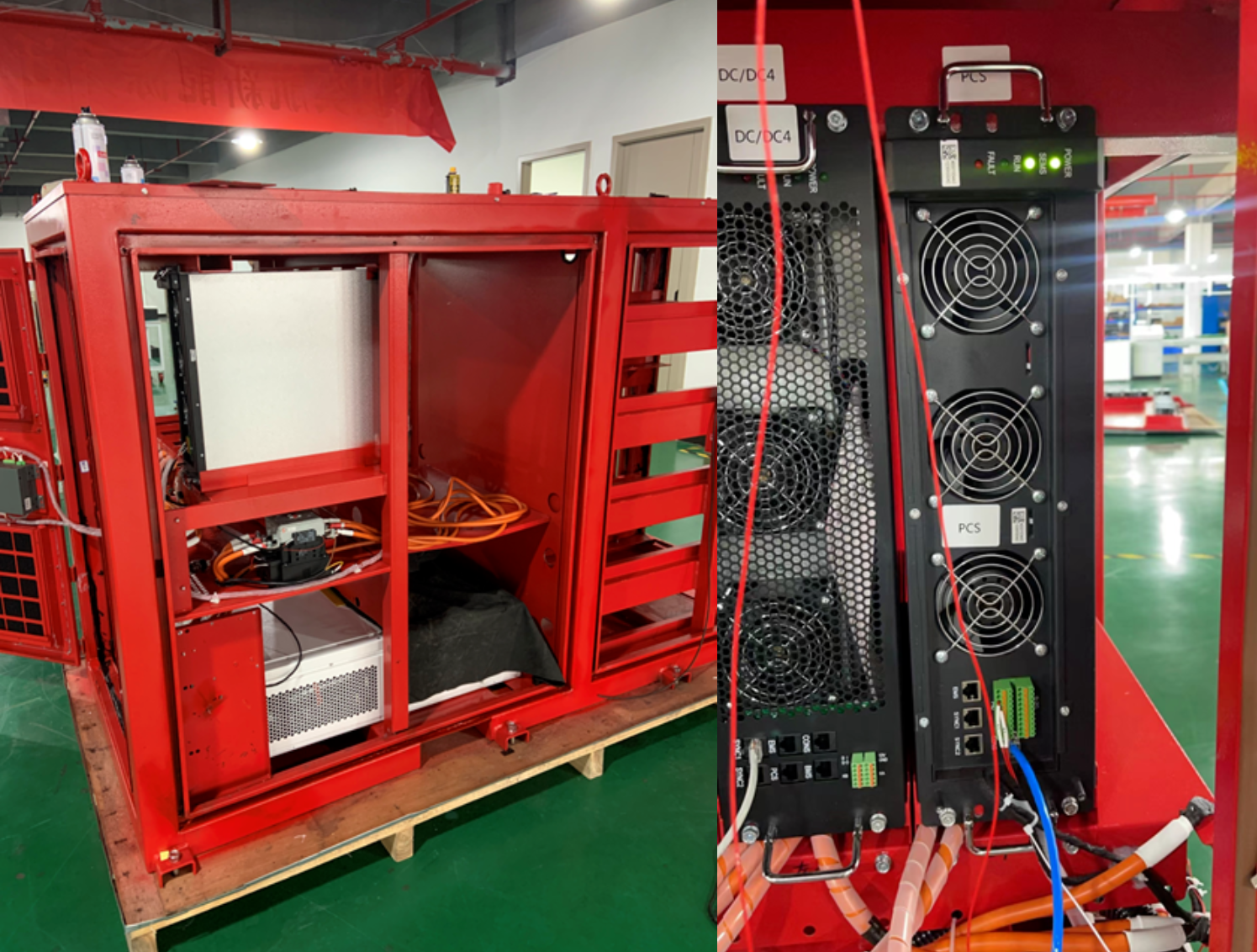
During hoisting operations, when high-power lifting is required, the PCS module of the grid power supply and the DCDC module of the battery pack will simultaneously supply power to the frequency conversion motor, ensuring the motor receives sufficient power to meet the demands of high-power lifting.
During lowering operations, the required power supply is relatively low. In this scenario, the PCS module of the grid power supply independently provides power to the motor, while automatically directing excess electricity from the grid to charge the battery pack via the DCDC module. This intelligent power management system ensures optimal energy utilization.
During lowering operations, the power demand remains relatively low. In this case, the excess energy from the grid is utilized to charge the battery pack via the PCS and DCDC modules. Additionally, the potential energy generated during descent drives the motor to act as a generator, and this recovered energy is also converted into electrical power for the battery pack through the DCDC module.
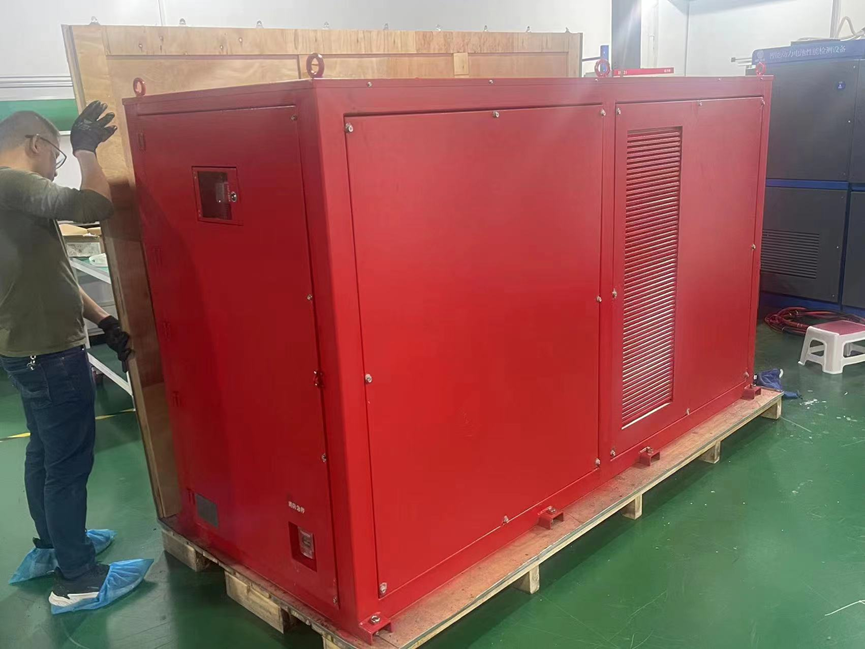
The energy storage system in this project has a capacity of 60kW/194.5kWh, equipped with one 60kW PCS module and four 60kW DCDC modules. The PCS and DCDC modules, developed by Yunt Power, feature fast response, strong overload capability, and robust grid adaptability. When paired with high-rate discharge batteries, the system can achieve a maximum discharge rate of 2C.
undefined